AluminumFibers
Update on the 3F2E project with the delivery of the first aluminum optical fibers.
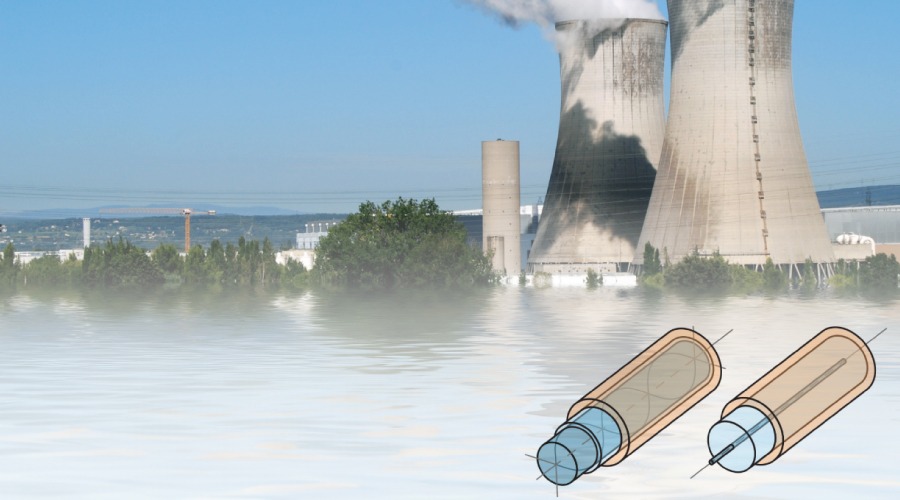
What is the 3F2E project?
3F2E (French Fiber Field for Extreme Environment) is a 100% French collaborative project led by a consortium of which SEDI-ATI Fibres Optiques is a member. It aims at developing radiation-resistant optical fibers (EXAIL), with metallic coatings (Photonics Bretagne), packaged (SEDI-ATI) for nuclear environment use. These fibers should be able to be integrated into “usual cases” close to existing needs (TechnicAtome & EDF).
The goal is to set up an integrated industry that is 100% Made in France, guaranteeing national sovereignty over a strategic technology.
There will be 3 different coatings delivered by the end of 2025:
- Aluminum coating
- Carbon + Copper coating
- Carbon + Polyimide coating
Photo at Photonics Bretagne of the fibre-drawing tower used to apply very special coatings. Credits: Photonics Bretagne.
The first French optical fiber with Aluminum coating
During the first part of the project, EXAIL developed preforms to manufacture radiation-resistant optical fibers (rad-hard, singlemode, gradded indes and step-index) for use in nuclear and high-temperature environments.
With its dedicated fiber-drawing tower, Photonics Bretagne was able to draw the first aluminum-coated fibers and obtain very positive results in term of linear attenuation and mechanical strength.
These fibers have been entrusted to SEDI-ATI Fibres Optiques to develop the seals and protections that are essential in extreme environments.
The role of SEDI-ATI Fibres Optiques in the project
In this project, we are requested by TechnicAtome and EDF to supply them with hermetic feedthroughs and All-Or-Nothing positioning systems that can whistand high temperatures, radiation and pressure.
Neutral gas brazing assembly
We already offer this type of assembly on conventional silica/silica fibers, and to date, we confirm that the brazing pre-tests we have carried out on this new aluminum fibers are conclusive. Visual and physical inspection has validated the fiber. We still need to carry out more advanced soldering tests and develop the various technological building blocks that will protect the fiber assemblies alone or in sensors for extreme environments (sealing, hermeticity, stress resistance).
To do this, we have, among other things, invested in an assembly enabling brazing to be carried out under neutral gas.
These new components will be promoted in the “fiber reinforced sensor” use cases for TechnicAtome and EDF.
In the remainder of the project, we will be developing the following technlogical building blocks for metal and polyimide-coated fibers:
- Brazing processes for the various metal coatings envisaged (Aluminum and Copper),
- Hermetic systems for connectors and outlets (windows and hermetic feedthroughs, cabling and electrical penetration) for polyimide fibers,
- Specific packaging (stainless steel tube).