PipeInspection
Optical fiber spool production for wire-guided robots
SEDI-ATI offers disposable ultra-lightweight and compact fiber optic spools directly mounted onto fiber-optic wire-guided crawlers for pipe inspection operations.
MajorConstraints
- Immersion in different types of liquids (sewed water, mud…),
- Mechanical strains (shocks, vibrations, radius of curvature),
- Allow both video and monitoring signals over long distances inside pipes.
TheChallenge
Need to transmit command signals to wire-guided robots and receive real-time video data over long distances inside pipes, where no radio frequency (RF) signals can pass.
Why inspect pipes?
Pipe inspection is essential to keep the structure in good condition. Inspections can detect cracks, leaks, corrosion, obstructions or sealing problems (joints and welds).
In addition to checking the integrity of the structure, they are also necessary from a regulatory and safety point of view, to avoid industrial accidents such as explosions or leaks of hazardous products. It is also mandatory to comply with current environmental and industrial regulations, which are regularly reviewed.
Complex inspections
The major challenge of these inspections is limited accessibility: pipelines and large pipelines are often buried, submerged or located in environments that are difficult to access, making them more laborious to inspect. All the more so when you consider the length and breadth of the network, which can extend over hundreds or even thousands of kilometers.
The inside of pipes is often under pressure, filled with fluids (water, oil, gas…) or subject to extreme temperatures, requiring solutions capable of withstanding these extreme environments. Traditional techniques such as video surveillance are not always sufficient.
Added to this is the possibility of signal or communication loss, since radio or GPS signals cannot effectively penetrate solid materials or water.
Dangerous practices for people and the environment
Previously carried out by humans, these pipe inspections directly exposed them to the material and human dangers associated with potential leaks or spills, which could result in injury or worse. What’s more, these practices were also highly restrictive, as the operating mode required the interruption of activity in these pipelines for several hours, and mobilized a large number of personnel.
It was therefore more than necessary to deploy new means of limiting human intervention: creating fiber-optic remote-controlled pipe inspection robots.
Inspecting with wire-guided vehicles
To ensure the safety of the operators, they no longer enter the pipe themselves, but use remote-controlled robots. They are electronically powered continuously, or by battery, and data transfer (camera feeds, sensors, etc.) requires a cable.
The first generations of pipe inspection robots were equipped with power cables and video feed transfer cables unwound from a winch. This technology meant that the robot had to retrace its steps to return to its base. The cable could jam, preventing the robot from being retrieved.
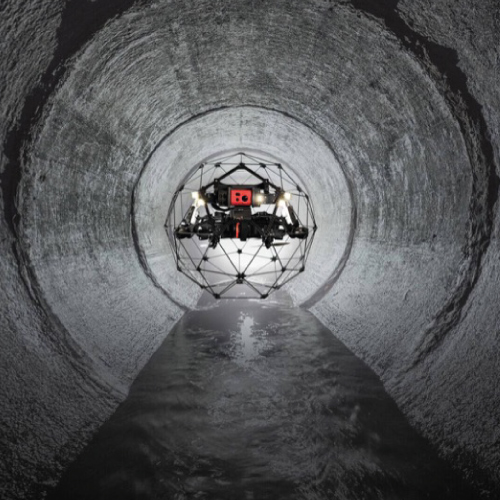
SEDI-ATIs deployable spools
The innovative solution proposed by SEDI-ATI Fibres Optiques is to mount a fiber optic deployable spool directly on the drone.
Unlike “conventional” winch technology, SEDI-ATI’s spool ensures a safe and rapid deployment of the fiber, unwinding as the robot moves. Here, the fiber doesn’t act like a “leash”, and the drone or wire-guided vehicle can enter at point A and exit at point B, or make any desired movement, without having to make the same journey back to base. The robot will never be hindered by the fiber if it gets caught somewhere.
As the spool is single-use, the fiber can be cut by the operator and left in the field (low pollution, as silica is actually sand). After initial use, the fiber can be reconnected by fusing a pigtail (a simple and common operation).
The range of deployable spools enables you to tackle any complex or extreme environment. Whether your robot is ground, underwater, aerial (drone) or hybrid, our spools can be easily adapted and mounted on the vehicle. Depending on the environment in which your robot will be operating, SEDI-ATI can supply spools in lengths of 1, 2, 5, 10, 20 or 30 kilometers.
SEDI-ATISolution
We offer a disposable ultra-lightweight and compact fiber optic spools, directly mounted onto the tethered robotic crawler.
It is the robot that deploys the optical cable by traveling through the pipe. Therefore, there is no traction nor any other mechanical force applied on the optical fiber.
We can design spools with different optical fiber lengths, depending on the distance to be travelled: 1, 2, 5, 10, 20 or 30 kilometers.
AdvantagesOf the SEDI-ATI solution
- The fiber-optic spool is directly integrated into the robot,
- Ease of installation on the robot,
- Travel distances up to 30 km from the launch point,
- Broad bandwidth for huge/heavy data transfer,
- The fiber optic cable can be left in the field to free the robot: no need to make the return trip, no risk to obstruct the robot.
Related products
Disposable amphibious fiber-optic spool for aerial and underwater applications [HAUV]
Discover the RBOB HAUV, a single-use amphibious spool directly mounted under your hybrid Aerial and Underwater drone, guaranteeing a secure and high-quality communication, even when moving from one environment to another.
Disposable fiber-optic spool for aerial applications [UAV]
The innovative concept behind our single-use fiber optic spool for aerial drones is that it is mounted directly under the drone.
Disposable fiber-optic spool for Unmanned Ground Vehicles [UGV]
The RBOB-UGV fiber optic spool is ideal for remotely controlling ground unmanned vehicles that have to operate in conditions where it is dangerous or impossible to have an onboard human presence, and where radio frequency signals are not permitted.
Disposable fiber-optic spool for Unmanned Underwater Vehicles [UUV-ROV]
The innovative concept of our disposable fiber optic spool for ROV lies in the fact that it is directly mounted onto the unmanned underwater drone.
Threaded hermetic adapter up to 30 bars
The KTRAV-IP series is a hermetic adapter for pressure applications up to 30 bars.